Cutting metals requires advanced industrial cutting technologies. However, it is important to consider the pros and cons of various industrial metal cutting techniques and compare them to the properties and durability of the metal to be cut.
Metal can be a tricky material to cut as some metals cannot be cut effectively using heat, while others, such as those that are electrically conductive, can be cut using plasma cutting, which applies high temperatures through a combination of electricity and ionized gas.
Therefore, the most commonly applied methods of metal cutting are plasma cutting and water jet cutting.
Plasma Cutting
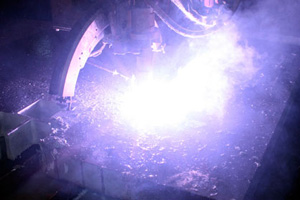
As mentioned, plasma cutting is a choice method for cutting materials that are electrically conductive such as copper, steel, aluminum and brass. Plasma is in its fourth state of matter when it is combined with electricity to form a powerful metal cutting force.
When plasma cutting was first introduced out of the plasma welding industry in the 1960s, it required the operation of highly advanced and slow running machines to render high precision cuts to metals.
As technology has advanced, plasma cutting machines are becoming more accessible to a wider range of people. Hobbyists and artists are using handheld plasma cutting torches in their own personal workshops to cut a variety of different materials and metals.
Plasma cutting offers the following benefits:
Water Jet Cutting
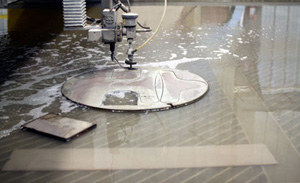
Water jet cutting is also frequently used to cut heavy metals. More and more industries are starting to rely on the effectiveness of water jet cutting over other industrial cutting methods.
Water jet cutting can cut more materials than virtually any other industrial cutting method, and is a very effective way of cutting metal.
Some metals do not respond well to cutting methods that require heat, as they are susceptible to thermal stress from high temperatures. Water jet cutting does not use heat. Instead, it employs a mixture of water and a non-toxic abrasive substance such as garnet or sand. The water jet stream is combined with compressed air and shot out at a velocity of three times the speed of sound.
As such, water jet cutting is capable of creating high precision cuts to a wide range of materials at high levels of thickness.
Water jet cutting can be applied on a multi-axis and the stream is very flexible. Therefore, it can produce uniquely cut designs and shapes to metals and can even render three-dimensional products.
Water jet cutting has an accuracy point of up to +/-0.001.h. and desired shapes and designs are plugged into a computer and applied to the metal using a robotic arm.
Finally, because water jet cutting is extremely precise, less expensive metal material goes wasted due to mistakes. It is also the most environmentally sound method of cutting metal. The water mixture can be used twice and there is no hazardous waste to dispose of after each metal cutting job.